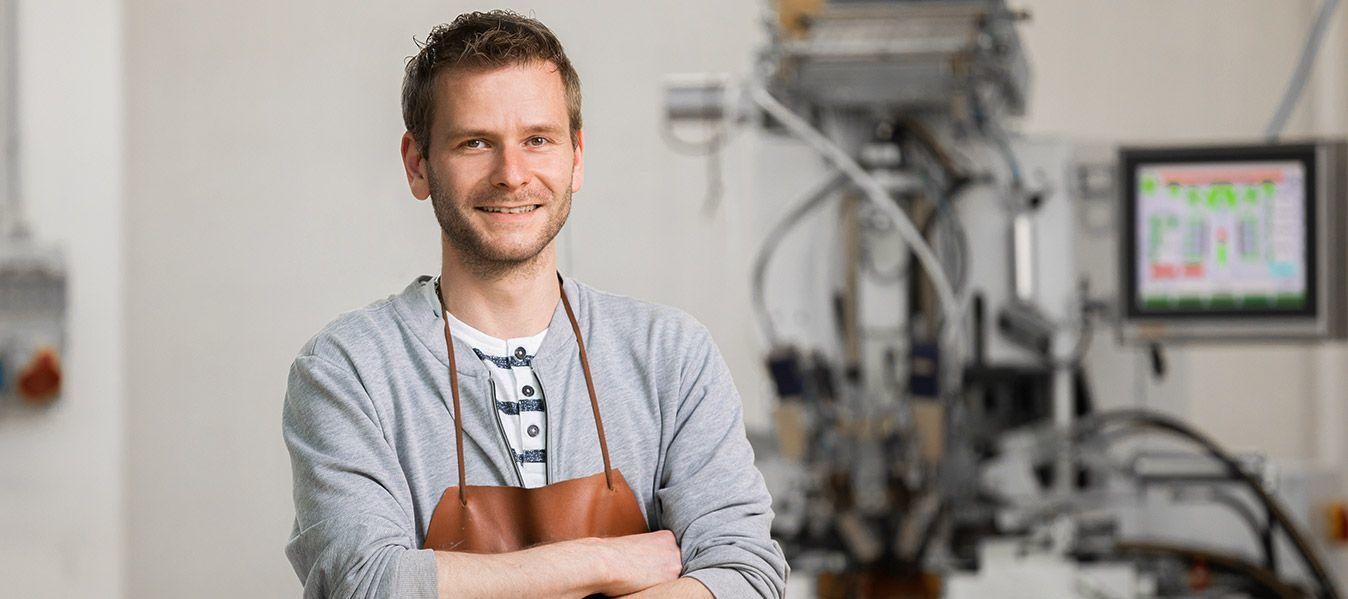
We contribute to CO₂-neutral leather production and support the reforestation project in Colombia. At the same time, we work exclusively with suppliers based in Europe. The majority of the leather we use comes from Germany and Italy. This avoids long transportation routes and reduces the carbon footprint in terms of sustainability.
Our suppliers mainly come from Germany, Italy, Spain and Portugal. We also attach great importance to sustainable materials from our textile suppliers, and some components are Ökotex certified. Many of our sole suppliers process some of the waste from the production process, which can then be reintroduced into the production cycle through appropriate treatment and used for new soles. Long-term and stable business relationships with our suppliers are important to us. We have been working with many of them for many years.
We select our production sites in accordance with our guidelines. Fair pay and long-term business relationships are particularly important to us. Our employees visit the respective production facilities directly on site at regular intervals. We have been working successfully with some of our external companies for decades. The topic of sustainability should also be constantly developed further. Wherever we can, we try to reduce CO₂ emissions through short transportation routes.
We only use high-quality leather in the production of our shoes and leave them as natural as possible. The materials used are mainly sourced from suppliers in Germany, Italy and Spain. The leather is checked “skin for skin” by specially trained employees. Only then is it sent to the headquarters in Schwanheim near the Alsace border. Further processing takes place at the Rhineland-Palatinate site and in small to medium-sized factories carefully selected by us.
Of course, the topic of sustainability also plays an important role in our development. For example, the soles of the H-Alina group have a recycled content of 30%, while the footbeds are made from 100% recycled material. The laces are made from the sustainable material Tencel, which is produced from certified, renewable raw materials.
WALDLÄUFER also lives up to its claim of creating shoes for sensitive feet when it comes to function: Be it velcro fasteners, elasticated straps or zippers. Customers can count on the proven WALDLÄUFER comfort without having to compromise on modern design.
The manufacture of a shoe requires the utmost precision and care. Every WALDLÄUFER starts with the design of a three-dimensional model. The creative fine-tuning then takes place on the computer. Gradings for all sizes and widths are produced on the basis of this design. Finally, the handmade WALDLÄUFER shoe is created with a great deal of technical expertise and sensitivity.
and-stitching shoes is the oldest traditional technique for joining leathers. Many of our WALDLÄUFER models are made using this traditional method. Our tailors sew the materials together with a thread in a laborious and time-consuming process. The classic hand stitching is much more durable than the now common machine stitching. The quality of the end product increases with every single step, from the design to the CAD pattern to the handcrafted finish – and a unique piece is created.
Tanning describes the process of preserving animal hides. Almost all WALDLÄUFER leathers are chrome-tanned – this is the most common type of leather processing. Chrome tanning is often associated with harmful substances, but this is a misconception. In fact, chrome III tanning is absolutely harmless. Unfortunately, chrome tanning does not have the best reputation, but it is the most environmentally friendly tanning method in terms of its CO2 balance.
In comparison, vegetable-tanned leather, for example, requires significantly more water. Environmental considerations are also relevant with regard to chrome tanning. For example, the tanning process produces waste water and residual materials containing chromium, which must be treated or recycled in order to recover valuable substances. Modern tanneries manage to bind up to 97% of the chromium used to the leather fibers in order to keep wastewater pollution as low as possible and save costs.